Services
Company Service and Production
Treatment of OBM Drill Cuttings using Solidification / Stabilization
WaterLise provides drill cuttings treatment services using Stabilization/Solidification process which are separate treatment techniques with similar goals where:
- Solidification of wastes involves the production of a solid mass having sufficiently high structural integrity to allow transport and /or disposal of the solid without requiring secondary containment. This technique converts hydrologic sensitive liquid and semi-liquids waste in physical form that can be stored safely and conveniently.
- Stabilization, however, involves the immobilization of constituents in wastes by chemical alteration to form insoluble compounds, or by entrapment within the solidified product.The stabilization /solidification systems provide an effective method for processing oil- base waste producing an environmentally safe, dry material that is acceptable for onsite, land farming disposal at an approved waste facilityThe most commonly used industrial system are cement based, silicate-based clay based and others.Both stabilization and solidification are classified as fixation processes applied to oil waste when the main purpose is to immobilize, isolate, or in some other way contain the contaminant from solids or semisolids waste.
In both cases the target is:
- Improve the handling and physical characteristics of waste.
- Reduce the surface area available for transferring or losing the contaminant andrestricting the fluid mobilization through the total volume of hard matrix.
- Reduce the contaminant’s solubility into the waste volume.
Treatment of OBM Drill Cuttings and Contaminated Sand using Indirect TDU
WaterLise provides drill cuttings and contaminated sand treatment services using other off-line methods such as thermal desorption process.
Thermal desorption is a cost effective and accurate environmental remediation technology that uses heat to increase the volatility of contaminants, so that they can be separated and removed from the solid matrix which typically is soil, oil-based mud drilling cuttings, sludge or filter cakes.
Thermal desorption is not incineration; the volatilized contaminants are either collected or thermally destroyed. A thermal desorption system therefore has two major components, the desorber itself and the off-gas treatment system.
The system has been uniquely designed and specifically customized for both short and long chain hydrocarbons that may be present in drilled cuttings by using a multiple shell dryer made of a stainless-steel alloy for higher cuttings discharge temperatures.
Before processing, the contaminated cuttings are weighed, then placed into a holding hopper equipped with a variable speed auger-feeder that measures the material fed into the rotary dryer at a rate up 5 m3 (wet) per hour.
The dryer unit is designed to dry and heat the contaminated cuttings indirectly so that burner combustion gases do not come in contact with the cutting or the hydrocarbon/ water gas stream. The externally heated rotary dryer is sealed on either end to limit oxygen entering the system and vapor exiting the system.
The dryer shell heats the cuttings to between 350 °C and 650 °C by conductive heat transfer. A special cleaning system in the dryer shell eliminates caking of solids and keeps the material agitated to allow for even heat transfer.
In order to guarantee vaporization of the water and hydrocarbons from the cuttings within the dryer, the cuttings stream must be thoroughly heated to the minimum temperatures required for complete vaporization of all liquid constituents.
Retention time within the dryer varies between 20-40 minutes depending on specific clean-up levels required. Processed inert cuttings leaving the dryer is mixed with recovered water for dust control, cooling and added moisture.
The vapors are routed to the baghouse, to remove the dust. The cleaned vapors are subsequently quenched and condensed through cooling sprays and by means of a shell and tube condenser with cooling tower. The recovered liquid is then passed through an coalescence oil/water separator.
The recovered water is used for re-hydration of the processed cutting, and for make-up water in the cooling tower. The recovered oil can be returned to the client for future use, or it can be used in the 20 MM BTU primary burners to heat the processes.
Air emission from the system meet or are below the norms set by the EPA 1990 Clean Air Act for Particulate Matter, SOx, NOx, and VOC’s. In fact, the EPA is designating this type of system as BDAT (Best Demonstrated Available Technology) for cleanup of hydrocarbon contaminated soils.
The TDU is designed to operate 24 hrs per day, with scheduled maintenance 2 days per month.
Solids Control Services
WaterLise provides solids control services and we supply high performance solids control equipment with different specification and capacity associated with professional engineering services to monitor and improve solids removal efficiency. Our solids control equipment includes but is not limited to the following:
▪ Flow Line Divider
▪ Gumbo/Primer Removal
▪ Shale Shakers Liner / Elliptical Motion ▪ Mud Cleaners / Desanders / Desilters ▪ Degassers
▪ Shale Shaker Screens
▪ Decanter centrifuges.
▪ Centrifugal pumps.
We provide Barite recovery systems onsite and we pair two centrifuges together, in which the first centrifuge targets solids between a 10 and 100μm range and the second purportedly removes those solids less than 10μm.
This 10 and 100μm range is the sweet spot within the particle size distribution curve for barite as highlighted below. The lower end of this range (10μm) is set by the centrifuge’s applied G-force, where the upper end of this range (100μm) is set by the practical suspended solids cut achieved by the primary solids control system, the flow line shakers.
The main purpose of barite recovery system is to:
▪ Reduce the content of drilled fines, specifically colloidal solids, and
▪ Perform barite recovery in order to reduce drilling fluid additive costs.
The lower end of this range (10μm) is set by the centrifuge’s applied G-force, where the upper end of this range (100μm) is set by the practical suspended solids cut achieved by the primary solids control system, the flow line shakers. The influent to the barite recovery centrifuge comes as a “slip-stream” from the active mud
system. This means that the full circulation volume of the Active Mud System is not sent through the centrifuge system. The first centrifuge’s solids “cake” is returned to the Active Mud System with the goal of recycling barite, where the centrate (containing the colloidal and ultrafine solids) is plumbed to the second centrifuge.
The second centrifuge is configured as a high-speed centrifuge to remove low gravity solids. The target range rests between the maximum capability of the centrifuge, relative to the maximum achievable G-force that can be applied (typically 2 to 5μm), and the lower range defined by the barite recovery centrifuge. The solids “cake” is considered waste and is disposed of, whereas the “cleaned” centrate is returned to the Active Mud System.
Drilling Waste Management Services
WaterLise offers a wide range of waste management services to minimize generated waste and contaminated discharged cuttings during drilling operations. This helps keep the environment clean and ensures that our operations are in compliance with the Algerian legislations.
We provide cost-effective and optimum solutions from environmentally acceptable procedures to achieve zero discharge plans and improve fluids recovery.
The outcome reduces operational costs and enables recycling. Among our waste management services, we provide cutting dryer centrifuges services onsite for the reduction of oil on cuttings (OOC% <5%), recovery of oil-based mud OBM fluids and reduction of volumes of waste to hall off for transportation and disposal by 40%.
The main benefits and features of our cuttings dryer centrifuges systems are:
- ▪ Reduction of oil on cuttings (OOC% < 5%) to meet environmental regulations.
- ▪ High-capacity unit is capable of supporting operations with a high rate ofpenetration (ROP) – average 40-60 TPH.
- ▪ Recovery of fluid alone may justify installation as 85% of recovered mud isreturned back to the active system after treatment with a Hi-“G” centrifuge.
- ▪ Reduces volumes of waste to haul off for transportation and disposal by 40%.
Brine Filtrations Services
WaterLise provide filtration services to our clients to help them meet their requirements, including cost-saving and avoiding related operational problems due to non-filtered fluids, especially across the pay zone.
We provide two-stage, skid mounted, easy to handle filtration vessels. The primary and secondary filtration stages are usually carried out together. We have filtered thousands of barrels on rig sites for reduced damage drilling as well as for under balanced drilling operations. The filtered fluid is stored in closed, clean frac tanks until used. We also provide best quality of polypropylene pleated cartridges and bags.
Liquid Mud Plant
WaterLise owns a Liquid Mud Plant (LMP) located in HASSI MESSAOUDE. The LMP occupied an area of 1500 m2 with capacity for storing up to 1400 m3 of drill mud and 520 m3 of fresh diesel. The LMP is designed for the fabricating/mixing and storage of Oil based drilling fluids (OBM). These products can be derived from various base fluids (brine and oil-based fluids) and can include further base materials which are dictated by the requirements of the well site. The liquid mud is fabricated, mixed and stored in a contained area and is transported to the wellsite.
Manufacture and Maintenance
Manufacture:
WaterLise is a leading manufacturer, based in Algeria, specialize in Solidification/stabilization unit and indirect thermal desorption plant, where was manufactured twelve (12) Solidifications unit and one (1) unit of indirect thermal desorption
Maintenance:
WaterLise provides a maintenance service, where we have workshop which contents on all equipment that meet the requirements of maintenance and renovations as well developing.
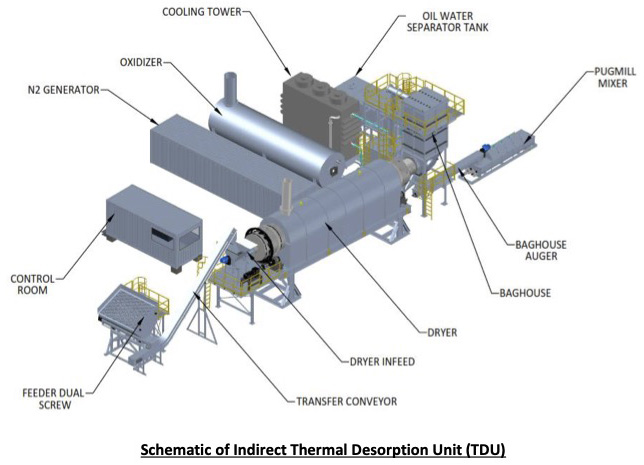
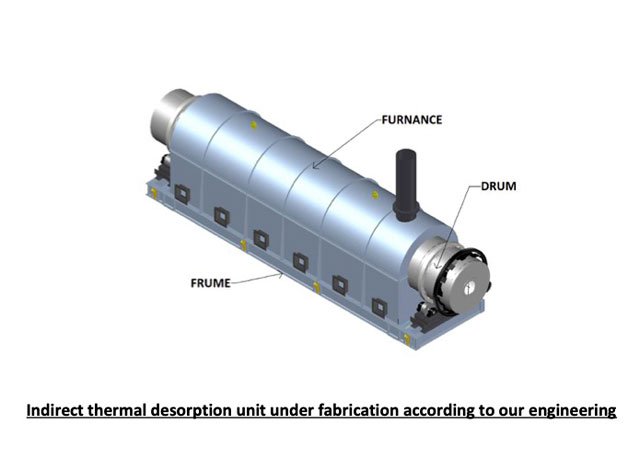
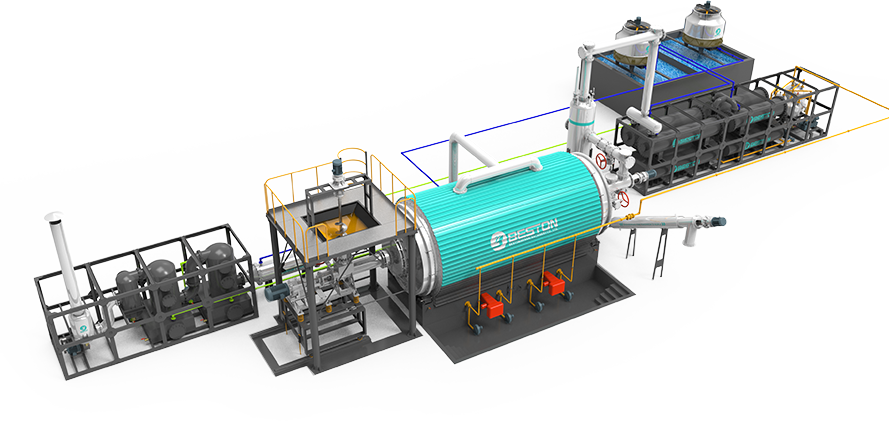
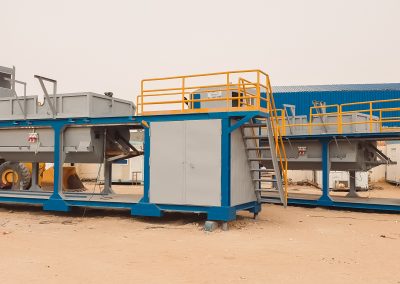
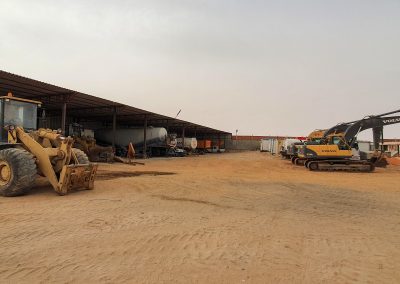
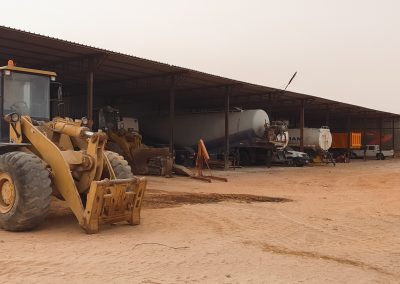
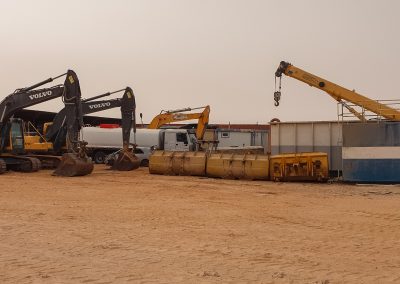
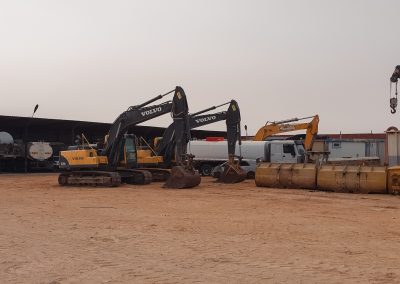
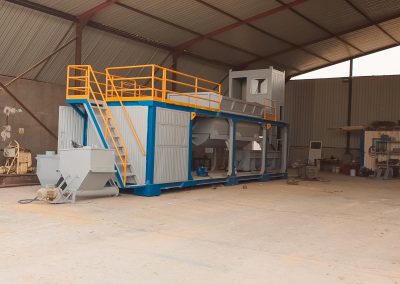
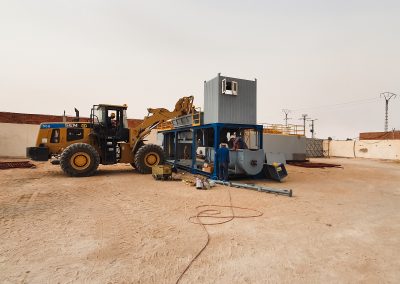
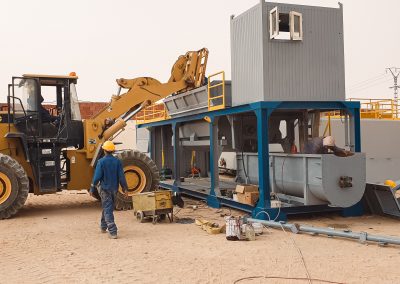
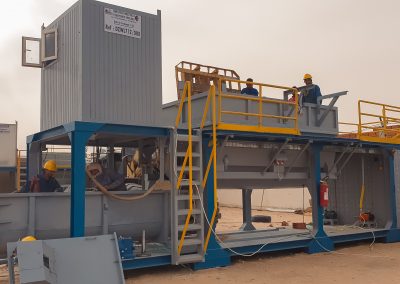
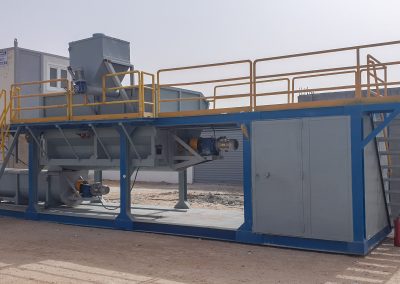